What is Lean Six Sigma? Lean Six Sigma is a combination of two powerful process improvement methods: Lean and Six Sigma. Lean and Six Sigma complement each other.
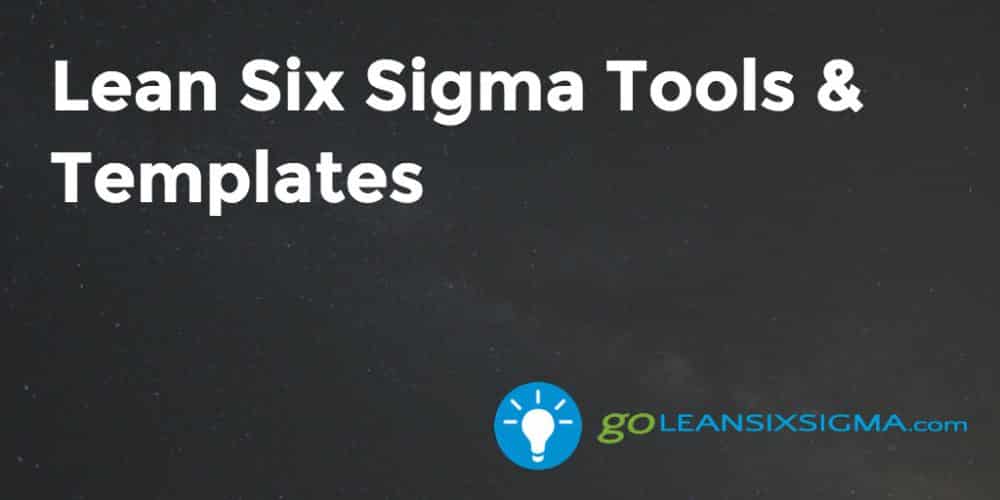
Six Sigma is defined as a method that provides tools to improve business process capabilities. Learn how to integrate lean and Six Sigma at ASQ.org. The Seven Basic Tools of Quality (also known as 7 QC Tools) originated in Japan when the country was undergoing major quality revolution and had become a m.
Lean accelerates Six Sigma, delivering greater results than what would typically be achieved by Lean or Six Sigma individually. Lean Six Sigma makes it easier for you and your teams to solve problems and increase the speed and effectiveness of any process within your organization.
You’ll be able to: Delight more customers. Minimize costs. Maximize profits.
Build better teams. At Go. Lean. Six. Sigma. com, our goal is to help you easily understand Lean Six Sigma so that you can apply it more easily.
Check out our Free Yellow Belt Training to start improving today! What is Lean? Lean is popular for its methodical approach to streamlining both manufacturing and service processes by eliminating waste while continuing to deliver value to customers. Although Lean is widely known for these benefits, it’s not just a set of tools. It stems from cultural roots which manifest in the business world as a particular approach to management: a Lean Culture.
A Lean Culture (also known as Lean Management) is the foundation of Lean process improvement. When a Lean Culture exists, improvement is exponentially more likely to be sustained and an environment for continuous improvement is created.
It is a combination of defining customer value, aligning around a common purpose, striving for perfection while at the same time respecting and developing employees. Lean originated with both Henry Ford and his storied assembly line and, more famously, with Taiichi Ohno who codified the Lean Management Philosophy and Practices into the Toyota Production System.
Free Six Sigma Green Belt Training Lessons! Your one click away! Six Sigma Digest unveils Green Belt Training. Grab our content, browse lessons, download data files.

A Lean process: Is faster. Is more efficient and economical.
Delivers satisfactory quality. Lean is achieved by removing “Waste,” which is activity not required to complete a process. After removing Waste, only the steps required to produce a product or service that is satisfactory to a Customer will remain. What is Six Sigma? Six Sigma is simply a method of efficiently solving a problem. Using Six Sigma reduces the amount of defective products manufactured or services provided, resulting in increased revenue and greater customer satisfaction.
Six Sigma identifies the cause(s) of your problem to efficiently develop effective solution(s). Six Sigma originated at Motorola in 1. What exactly does “Six Sigma” mean? Six Sigma is named after a statistical concept where a process only produces 3. DPMO). Six Sigma can therefore be also thought of as a goal, where processes not only encounter less defects, but do so consistently (low variability). Basically, Six Sigma reduces variation, so products or services can be delivered as expected reliably.
What are the benefits of using Lean Six Sigma? Organizations face rising costs and increasing competition every day. Lean Six Sigma allows you to combat these problems and grow your business the following ways: Lean Six Sigma Increases Profit. Lean Six Sigma increases your organization’s revenue by streamlining processes. Streamlined processes result in products or services that are completed faster and more efficiently at no cost to quality.
Simply put, Lean Six Sigma increases revenue by enabling your organization to do more with less – Sell, manufacture and provide more products or services using less resources. Lean Six Sigma Decreases Costs. Lean Six Sigma decreases your organization’s costs by: Removing “Waste” from a process. Waste is any activity within a process that isn’t required to manufacture a product or provide a service that is up to specification.
Solving problems caused by a process. Problems are defects in a product or service that cost your organization money.
Basically, Lean Six Sigma enables you to fix processes that cost your organization valuable resources. Lean Six Sigma Improves Efficiency & Effectiveness. Lean Six Sigma improves the efficiency and effectiveness of your organization by: Maximizing your organization’s efforts toward delivering a satisfactory* product or service to your customers.
Allowing your organization to allocate resources/revenue produced from your newly improved processes towards growing your business. Simply put, Lean Six Sigma enables you to create efficient processes so that your organization can deliver more products or services, with more satisfied customers than ever before. Lean Six Sigma Helps Develop People/Employees. Lean Six Sigma develops effective people/employees within your organization by: Involving employees in the improvement process. This promotes active participation and results in an engaged, accountable team.
Building trust. Transparency throughout all levels of the organization promotes a shared understanding of how each person is important to the organization’s success. Basically, Lean Six Sigma develops a sense of ownership and accountability for your employees. This increases their effectiveness at delivering results for any improvement project they are involved in.
Quite often, this benefit is overlooked by organizations who implement Lean Six Sigma, but it’s underlying advantages dramatically increase the chances of continued success of Lean Six Sigma, and your business. How does Lean Six Sigma work? Lean Six Sigma is simply an effective methodology used to fix a problem. It is based on common sense practices and is completed in five phases: Five Basic Phases.
Define: Define the problem and what is required to satisfy your customer. Measure: Map the current process to collect data. Torrent Signal Processing First Textbook on this page. Analyze: Investigate and identify what causes the problem. Improve: Implement a fix that will solve the problem.
Control: Sustain the improved results. Simply put, Lean Six Sigma helps you identify the cause of a problem and implement a fix based on facts, rather than assumptions. This produces improved results and success that you and your team, managers and organization can be proud of. Who benefits from using Lean Six Sigma? Organizations Of All Sizes. Lean Six Sigma works for small, medium (SMBs) and large businesses.
In fact, often times, the same success that is achieved within large businesses can be achieved in small and medium businesses since smaller organizations can move faster because less people, fewer resources and lower levels of red- tape are involved. The benefits are boundless, as Lean Six Sigma increases revenue and reduces costs, while freeing up resources that can be utilized toward any endeavor your organization wishes to pursue. For example: A new product or service.
Other improvement projects. Expanding your sales force. People & Morale. Lean Six Sigma not only increases revenue and reduces costs, it positively affects people by engaging them in improving the way they work. Since employees are the closest to the actual work (production of a product or delivery of a service) of any organization, they become the best resources to understand how to improve the efficiency and effectiveness of business processes. By participating in successful Lean Six Sigma projects, employees are able to build the confidence and develop the capability to become your business’ most important assets.
Studies show that when employees feel that they have a positive affect on the organization, they perform better, are more accountable and live happier lives. And once your employees get comfortable with Lean Six Sigma skills, they can continue to find and remove problems and waste in your organization. Industries. Healthcare.
Healthcare costs are skyrocketing across the country and an aging population means increased stress on healthcare services. Lean Six Sigma can help you increase the amount of time care providers are able to spend with patients, reduce the time spent on paperwork, and reduce the time people spend waiting for care, waiting for claims or waiting for a call.
Technology. As consumers increasingly rely on technology, Lean Six Sigma helps businesses by delivering products with fewer defects, decreasing returns and more.
What Is Six Sigma? Six Sigma is a disciplined, data- driven approach and methodology for eliminating defects (driving toward six standard deviations between the mean and the nearest specification limit) in any process – from manufacturing to transactional and from product to service. The statistical representation of Six Sigma describes quantitatively how a process is performing. To achieve Six Sigma, a process must not produce more than 3. A Six Sigma defect is defined as anything outside of customer specifications. A Six Sigma opportunity is then the total quantity of chances for a defect. Process sigma can easily be calculated using a Six Sigma calculator.
The fundamental objective of the Six Sigma methodology is the implementation of a measurement- based strategy that focuses on process improvement and variation reduction through the application of Six Sigma improvement projects. This is accomplished through the use of two Six Sigma sub- methodologies: DMAIC and DMADV. The Six Sigma DMAIC process (define, measure, analyze, improve, control) is an improvement system for existing processes falling below specification and looking for incremental improvement. The Six Sigma DMADV process (define, measure, analyze, design, verify) is an improvement system used to develop new processes or products at Six Sigma quality levels. It can also be employed if a current process requires more than just incremental improvement.
Both Six Sigma processes are executed by Six Sigma Green Belts and Six Sigma Black Belts, and are overseen by Six Sigma Master Black Belts. According to the Six Sigma Academy, Black Belts save companies approximately $2. GE first began Six Sigma in 1. Motorola and Allied Signal blazed the Six Sigma trail. Since then, thousands of companies around the world have discovered the far reaching benefits of Six Sigma.
Many frameworks exist for implementing the Six Sigma methodology. Six Sigma Consultants all over the world have developed proprietary methodologies for implementing Six Sigma quality, based on the similar change management philosophies and applications of tools. New to Lean Six Sigma?